Most read
- 1. Danobatgroup sets a new turnover record of €344 M in 2024
- 2. Danobat revolutionizes manufacturing with a new precision robot
- 3. MONDRAGON expands its digital presence with Bluesky
- 4. MONDRAGON leads ASETT, the Social Economy Hub for social transformation
- 5. Orbik Cybersecurity, the first technological start-up to become a co-operative
- 6. Eika acquires Stone Cooker S.L and its innovative 'Suiseki' table to boost growth
New hub for industrial digitalisation and grinding in the Basque Country
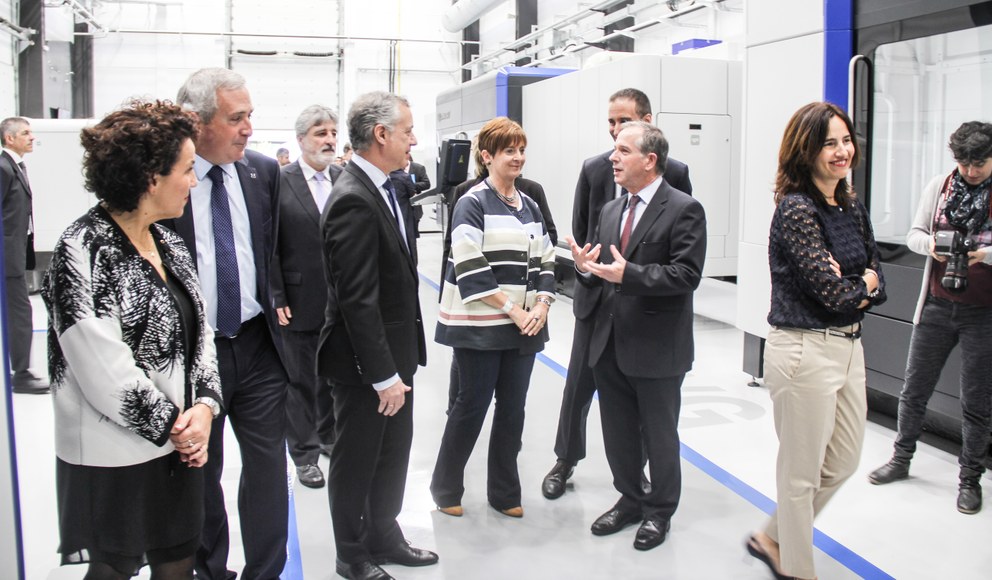
With the aim of promoting the transfer of advanced technologies to companies and strengthening the competitiveness of industry, the Basque technology centre specialising in Advanced Manufacturing IK4-IDEKO and the industrial group DANOBATGROUP have inaugurated the Digital Grinding Innovation Hub (DGIH), the new hub of the Basque Country for research and development of innovative solutions in digitalisation and grinding technologies.
The opening ceremony, which was presided over by the President of the Basque Government, Iñigo Urkullu Renteria, was also attended by the Minister for Economic Development and Infrastructure, Arantxa Tapia, and the Deputy for Economic Development, Rural Environment and Territorial Balance of the Provincial Government of Gipuzkoa, Ainhoa Aizpuru, among other authorities.
With an investment of in excess of 6 million Euros in equipment, the DGIH is a collaborative space focused on the experimentation, demonstration and validation of research projects
Also present at the event were the General Manager of DANOBATGROUP, Pello Rodríguez, the General Manager of IK4-IDEKO, Nerea Aranguren, and the President of the MONDRAGON Corporation, Iñigo Ucín.
With an investment of in excess of 6 million Euros in equipment, the DGIH is a collaborative space focused on the experimentation, demonstration and validation of research projects aimed at industrial digitalisation and grinding technology.
The digital revolution or industry 4.0 has resulted in the implementation of Internet-based technologies in production plants with the aim of making smart and interconnected factories. In this context, all the equipment of the Digital Grinding Innovation Hub will be connected allowing remote and real-time access to the information coming from the machines and the machining process.
"Within this digitalisation environment, we will work on systems for the characterisation of the condition of machine components, the optimisation of variables that influence the machining processes and energy consumption. Hence, it will be possible to anticipate failures and to activate predictive maintenance strategies and experiment with alternatives that save energy and reduce the environmental impact," says Aranguren.
Equipped with state-of-the-art machinery, the activity of the DGIH also focuses on research into grinding technologies, the most critical phase in the manufacturing processes of industrial parts and components in strategic sectors such as power generation, rail transport, aeronautics and capital goods.
The hub also aims to carry out R&D into the manufacture of new materials and special alloys, grinding of complex shapes and geometries, optimisation of cooling, diamond grinding technology and ecological grinding.
Among the objectives of this space is also the training of new professionals for the digital industry who, in addition to understanding the operation of the machines, are able to interpret and analyse the information from manufacturing processes obtained through data collection devices.
To guarantee its operation, the new Digital Grinding Innovation Hub will be equipped with the latest generation of DANOBAT machinery, SORALUCE multi-function milling machines and FAGOR AUTOMATION equipment specialised in advanced data acquisition, among other machines that will be added during the course of the project.
Cooperation as the key to success
The Digital Grinding Innovation Hub is a completely open project that seeks to promote collaboration and synergies between technology centres, universities, companies, suppliers, users, SMEs and start-ups involved in the value chain of industrial grinding and digitalisation processes.
The space, which will be used for testing and trials of solutions that are very close to industrialisation stages, is a multilocation project, which, in addition to the IK4-IDEKO facilities, has ramifications in other spaces such as the University of the Basque Country (UPV/EHU), the Mondragon University or the Machine Tool Institute (IMH), entities that collaborate in this project.
The hub can count on the support of several agents of the Basque Network of Science, Technology and Innovation such as CFAA, CEIT-IK4 or AOTEK. While organisations such as EKIN, Unnesa or Korta Group have shown their support for a space that will allow them to have a permanent demonstration that works in real manufacturing conditions.
"All these agents will join their capacities to build a space aimed at the search for national and international alliances that allow us to remain at the forefront of industrial manufacturing. It is a project under construction and open to equipment manufacturers, component suppliers and machining specialists,” Aranguren adds.
The initiative also counts on the cooperation of international entities specialised in high value added industrial manufacturing such as the German company SCHAEFFLER, SAINT GOBAIN in France, TYROLIT in Austria or the University of Bremen in Germany.
For his part, the general manager of DANOBATGROUP, Pello Rodríguez, considers that "the DGIH will serve to reinforce the positioning of the Basque Country, or Euskadi if you prefer, as an important pole in the development of grinding technology aimed at high value added manufacturing processes, to favour a Basque business fabric for better competitiveness through the development of differentiated, technologically advanced, sustainable products and services featuring innovative concepts.
The support of a benchmark industry
The creation of centres of excellence such as the DGIH to promote research into advanced technologies applied to industrial manufacturing is part of the commitment of DANOBATGROUP - an industrial group with leading companies in the field of advanced manufacturing such as SORALUCE and DANOBAT - to be at the forefront of changes in the sector through the development of advanced solutions with major innovation elements
The group, which invests 8% of its annual revenues in R&D&I, has previous experience in this field, such as the SORALUCE centre of excellence in Germany, a space created with the mission of developing milling and turning technologies.
About IK4-IDEKO
The Basque Technological Centre IK4-IDEKO has a long-standing experience of 30 years in research, development and innovation of new technologies applied to industrial manufacturing.
Set up to respond to highly technological challenges from the MONDRAGON Corporation machine tool companies, today it has more than 100 researchers and a portfolio of more than 50 customers a year.
Its R&D&I is aimed at offering innovative solutions to improve competitiveness of the business fabric, and is structured in 4 research units: Dynamics and Control, Manufacturing Processes, ICT and Automation and Design and Precision Engineering.
About DANOBATGROUP
The industrial group DANOBATGROUP, the machine tool division of the MONDRAGON Corporation, specialises in the manufacture of solutions for high value added components, turnkey production systems and technologically advanced services.
With a staff of 1,300 people, it develops full solutions for strategic sectors such as the railway, power generation or aeronautics sectors.