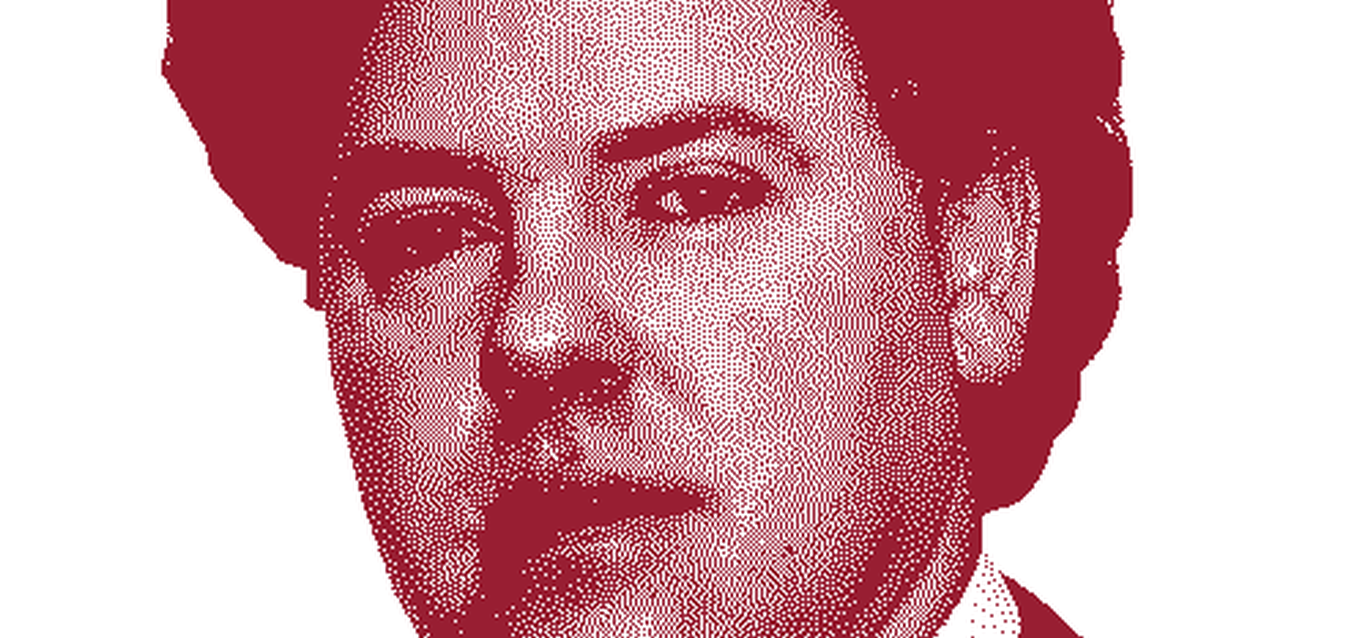
A propósito de la Industria 4.0
En este sentido, el fenómeno de la Industria 4.0 está adquiriendo todos los rasgos de un paradigma en construcción, conforme a la definición aportada por Peter Drucker, una de las figuras más reconocidas de la gestión empresarial moderna, quien afirmaba que “los paradigmas de las ciencias sociales, como es la gestión empresarial, constituyen las asunciones básicas sobre la realidad. Sin embargo, a pesar de su importancia, tales asunciones son rara vez analizadas, estudiadas y puestas en entredicho. De hecho, rara vez se explicitan.” De forma equivalente, cuando se habla del concepto de Industria 4.0, cada interlocutor lo interpreta de una forma diferente, sin que ello signifique necesariamente que se comprende el fenómeno: conforme a los análisis efectuados por la Federación de Industrias alemanas, únicamente el 12% de las empresas alemanas afirman sentirse preparadas para afrontar la Industria 4.0.
En realidad Industria 4.0 constituye un paradigma revisitado: ya en la década de 1980 conocimos el fenómeno de la Fabricación Integrada por Ordenador (Computer Integrated Manufacturing - CIM) y vimos a empresas como General Motors que lideraba el desarrollo del Protocolo de Fabricación Automatizada (Manufacturing Automation Protocol- MAP), fiarlo todo a la automatización a ultranza, pretendiendo que la robótica iba a resolver sus problemas crónicos de relaciones laborales, llegando a la creación de una empresa conjunta con el proveedor de robótica FANUC o la adquisición de la sociedad de servicios informáticos EDS.
Diez años más tarde, las investigaciones desarrolladas por el Instituto de Tecnología de Massachusetts–MIT, consolidadas en el célebre libro La máquina que cambió el mundo, evidenciaron que la competencia japonesa obtenía mayores productividades en sus plantas de fabricación con una menor intensidad de capital invertido, es decir con menores niveles de automatización. Entretanto, General Motors sufría una auténtica hemorragia de participación de mercado, perdiendo 19 puntos de cuota de mercado, y con ello la primacía mundial entre los fabricantes de automóviles.
En contraposición, Ford llevó a cabo un proceso de transformación más holístico e integral, partiendo de la visión de que la competitividad era la resultante de múltiples factores, y no exclusivamente de la productividad de las actividades directas de manufactura.
Como resultado, Ford desarrolló una estrategia integral de transformación que consideraba el diseño del producto, el aseguramiento de la calidad o la gestión de los proveedores. Ya entonces los estudios comparativos llevados a cabo por la consultora McKinsey establecían que dos tercios del diferencial competitivo de las empresas más eficaces con respecto a su competencia radicaban en la productividad de las actividades indirectas de gestión.
Conforme documentan los análisis llevados a cabo por McKinsey sobre la evolución competitiva de la industria americana de automoción, Ford fue capaz de igualar la productividad de plantas japonesas en los Estados Unidos cinco años antes que General Motors.
Volviendo a la actualidad, recientemente la Academia Nacional Alemana de Ciencia e Ingeniería ha publicado el informe Industria 4.0: estudio comparativo internacional, opciones de futuro y recomendaciones para la investigación en manufactura. El estudio constituye un análisis sobre la situación de las economías occidentales en la implantación de la Industria 4.0. Conforme a la visión aportada por ACATECH, una de las debilidades más relevantes de la industria alemana radicaría en su insistencia en el desarrollo de los modelos de negocio tradicionales (fundamentalmente basados en sus destrezas de ingeniería y tecnologías de manufactura).
El foco de la industria alemana estaría concentrado en las soluciones para los procesos industriales y presentaría importantes carencias competenciales en el ámbito de Internet y de las tecnologías en red, susceptibles de lastrar su capacidad de adaptación a las exigencias de la digitalización. Adicionalmente, el énfasis en la ingeniería hace que las soluciones alemanas tiendan a ser ingenierizadas en exceso y dotadas de una elevada sofisticación. La academia alemana alerta que estos desarrollos, orientados al mercado interior, no están alineados con las necesidades de los mercados globales y en consecuencia, son susceptibles de ser atacados desde posiciones más pragmáticas y menos onerosas.
Sorpresivamente, el Informe de ACATECH aporta una breve reseña del perfil de Euskadi en el ámbito de la Industria 4.0. Así, si bien reconoce la potencia industrial vasca, su capacidad tecnológica y competencia profesional, reseña como debilidades más destacadas su aproximación a la Industria 4.0 desde una orientación altamente tecnocéntrica y su obsesión por la generación de ventajas competitivas mediante la aplicación de la tecnología, al tiempo que destaca que su debilidad básica radica en las limitadas capacidades para la innovación en modelos de negocio y los servicios.
Estrategia vasca para la Industria 4.0
Interpretando el diagnostico de ACATECH, cabría afirmar que la estrategia vasca para la Industria 4.0, en escala reducida, presentaría algunas de las manifestaciones del mal alemán, que consistiría en abordar la construcción del nuevo paradigma tecnológico a partir de una perspectiva anticuada. Y es que en Euskadi se tiende a traducir el concepto Industria 4.0 por Taller 4.0 y pretendemos resolver nuestros problemas de competitividad incrementando la intensidad tecnológica aplicada a los procesos directos de fabricación (por ejemplo, estampación, mecanizado, montaje, etc). Y ello a pesar de que los análisis actualizados ponen de manifiesto que, a día de hoy, el trabajo directo de manufactura apenas representa el 50% del empleo total del sector industrial. Así, de los 17,2 millones de persona empleadas por la empresas industriales americanas, prácticamente 10 millones llevan a cabo tareas indirectas.
Quiere ello decir que si se focalizan las iniciativas de innovación tecnológica en los procesos productivos directos, sólo estaremos trabajando sobre una fracción del diferencial competitivo existente con relación a las empresas más avanzadas. Ya en 1994, James Utterback, profesor– investigador de la MIT Sloan School of Management, ilustró en su clásico libro Dinámicas de la innovación tecnológica que las industrias, en la madurez de su evolución tecnológica, tienden a concentrarse en el desarrollo de innovaciones de proceso de carácter incremental.
Este mismo año 2017, la investigadora de la Universidad de Washington Anne Marie Knott ha dado a conocer los resultados de una investigación que ratifican el pronóstico de James Utterback, al tiempo que evidencia que la I+D en industrias ya establecidas sufre una progresiva pérdida de productividad hasta generar resultados marginales.
Según Anne Marie Knott, el progreso global en la innovación que experimenta la sociedad se explica o bien como consecuencia de la aparición de innovaciones disruptivas que dan lugar a nuevas industrias o bien porque las empresas ya establecidas aplican su conocimiento en ámbitos ajenos a sus sectores de origen.
Estos resultados han sido confirmados por la investigación desarrollada por un equipo mixto de investigadores de la Universidad de Stanford y el Instituto de Tecnología de Massachusetts – MIT, publicada en marzo de 2017. La investigación realizada en diversos sectores de actividad (industria, medicina, agricultura…) arroja la conclusión de que la productividad de la investigación científica en una disciplina concreta tiende a decrecer de forma pronunciada con el paso del tiempo.
Como ilustración, la industria de la microelectrónica precisa en la actualidad de equipos de investigación 75 veces mayores que en la década de los años 70 para poder seguir cumpliendo la famosa Ley de Moore, por la cual la densidad de integración de transistores en los chips se dobla cada dos años. Si sumamos los efectos combinados de estas observaciones, las advertencias de ACATECH adquieren plena significación: en el desarrollo de la Industria 4.0, la obsesión por la aplicación de las tecnologías en los procesos directos de manufactura se traducirá en un rendimiento decreciente de la inversión en I+D y tendrá un impacto limitado en la competitividad industrial. Cabe preguntarse por tanto sobre cuál sería la estrategia más adecuada para abordar el desarrollo de la Industria 4.0 en el caso vasco. Para ello es preciso tener en cuenta la observación de Albert
Einstein, quien afirmaba que… “Si buscas resultados distintos, no hagas siempre lo mismo.” En consecuencia, una primera tarea a afrontar es ayudar a nuestras empresas a mejorar su comprensión del fenómeno Industria 4.0., de forma que puedan interpretar éste paradigma tecnológico en términos de negocio y detraer consecuencias concretas en materia de estrategia y gestión empresarial.
Perspectiva holística
En esta labor es preciso recuperar la formulación original del concepto Industria 4.0 y abordar su desarrollo desde una perspectiva holística, de forma que integre los tres ejes de articulación del paradigma: la digitalización e Integración horizontal y vertical de las cadenas de valor, la digitalización de la oferta de productos y servicios, así como la articulación de modelos de negocio digitales. Es decir, superar la perversión de interpretar la Industria 4.0 como sinónimo de Taller 4.0.
Los ejemplos de General Motors y Ford evidencian la trascendencia que adquiere la comprensión estratégica del empleo eficaz de las tecnologías en la gestión industrial y su impacto en la competitividad final de las empresas.
Finalmente, es preciso abordar el déficit competencial que presentan las empresas vascas en materia de innovación en modelos de negocio y servicios, tal y como refiere ACATECH. Para ello será necesario desarrollar nuevas capacidades técnicas y de gestión para incorporar modelos innovadores de negocio en el ámbito de la manufactura, y particularmente, desarrollar competencias en el ámbito de la innovación en los servicios y la transformación digital.
En caso contrario la industria vasca es susceptible de repetir aquel pasaje histórico que relata la decadencia inexorable de los clippers a pesar del incremento de las innovaciones incorporadas en estas embarcaciones como respuesta a la aparición de los barcos a vapor. A la postre, la competición por el transporte marítimo transatlántico estaba perdida para la navegación a vela ante el cambio radical de paradigma que implicaba la tracción a vapor.